Active vibration damping of a machining robot with hybrid drive
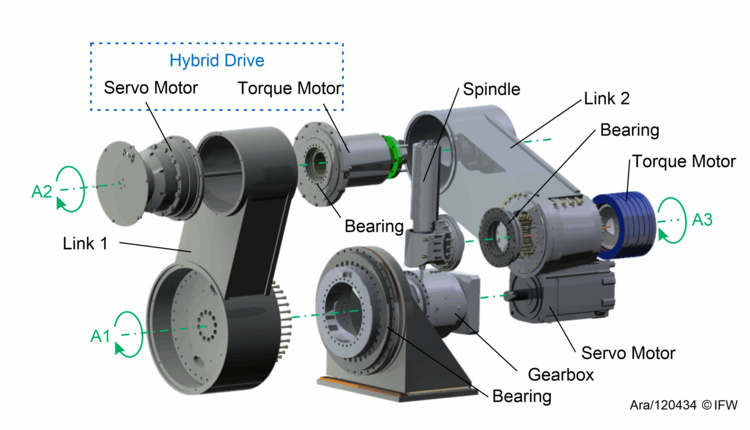
E-Mail: | araoud@ifw.uni-hannover.de |
Team: | Taha Araoud |
Year: | 2023 |
Funding: | German Research Foundation – DFG |
Duration: | 10/23 - 07/26 |
The increasing use of industrial robots in machining promises flexibility and cost-efficiency. However, this comes with challenges such as low gearbox stiffness and susceptibility to vibrations in the robot axes. In contrast, machine tools offer higher precision but are significantly more expensive to purchase. Against this background, we have already conducted several studies on robotic machining.
Objective of the project
The project “Active Vibration Damping of a Machining Robot with Hybrid Drive” (ASK-ROB) aims to develop a model-based control method for active vibration damping. This is intended to improve the machining accuracy of industrial robots.
Advantages
- use of industrial robots in machining – increased flexibility and cost-efficiency
- active vibration damping using an additional actuator – improved machining accuracy
Procedure
The Innoflex robot developed at our institute features higher stiffness compared to conventional industrial robots, achieved through its design and the use of a WITTENSTEIN Galaxie® gearbox. Equipped with three rotary axes and one linear axis, the Tool Center Point (TCP) can be aligned across various spatial planes. A key element of the robot’s kinematics is the second rotary axis, actively stiffened by a hybrid drive concept combining a gearbox and torque motor, increasing static stiffness tenfold compared to conventional drives.
Our project focuses on developing a model-based control method for active vibration damping (AVD) of the robot structure. The nonlinear, pose-dependent vibration behaviour is considered by creating a multidimensional multi-body model of the robot. Control parameters are adapted to the specific robot pose. A special focus is placed on decoupling the two controllers of the hybrid drive. Finally, machining tests will be conducted to evaluate the control method’s potential in the machining process.
Are you also interested in a cooperation project?
Contact Mohamed Taha Araoud via e-mail at araoud@ifw.uni-hannover.de or by phone at +49 511 762 18340.