Force-sensitive guidance systems based on directly deposited component-specific sensors
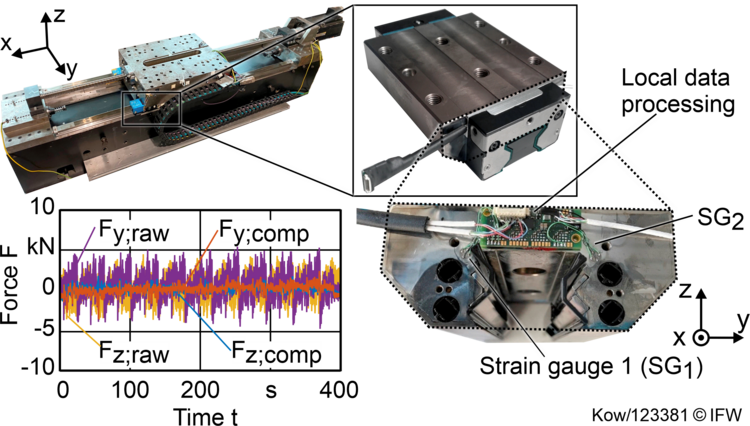
E-Mail: | kowalke@ifw.uni-hannover.de |
Team: | Dennis Kowalke |
Year: | 2021 |
Funding: | German Research Foundation - DFG |
Duration: | 04/21 - 11/24 |
Forces are an important source of information for process and condition monitoring in machine tools. Structure-integrated force measurement makes it possible to measure forces without negatively influencing machine properties such as stiffness or workspace size. However, previous approaches to structure-integrated force measurement have not been able to establish themselves, as they are associated with a high level of integration effort and costs.
These development costs are often not affordable for machine manufacturers. If a structure-integrated force measurement is carried out with common and standardized machine components, a structure-integrated force measurement is possible without complex adaptation of the machine structure. Components that are located in the force flow between the workpiece/tool contact and the machine bed are suitable for this. Due to the high demands on accuracy, these components are designed to be highly rigid. The low elongation caused by the high rigidity has so far prevented structure-integrated force measurement with such components.
Objective of the project
In order to simplify the structure-integrated measurement of forces in machine tools, we are researching the ability of profiled rail guides for structure-integrated force measurement. To this end, we apply strain gauges to the guide shoes using directly deposited thin-film sensors and supplement them with integrated signal amplification. This retains the standardized external geometries of the guide system and, at the same time, provides the strain signals in a standardized signal range for industrial control technology.
By directly depositing the sensor structures, we achieve great freedom in the design of the sensor layout and the connection points. We also dispense with polymer carrier foils that are subject to aging. In order to increase the quality of the measured force, we are researching methods of sensor data fusion and self-calibration.
Advantages
- Measurement of process forces - integrated monitoring of all machining processes without changing the machine properties
- Identification of damage and wear - Evaluation of the component condition (for example after collisions)
Procedure
In this project, we are working with the Institute of Microproduction Technology, Bosch Rexroth AG and Fooke GmbH to research a force-sensitive profile rail guide for structure-integrated force measurement. We increase the measurement accuracy by using component-specific sensor layouts and materials and by dispensing with conventional adhesive and carrier film intermediate layers. We also use compensation approaches to separate the constraining forces inherent in the structure from the process forces.
Are you also interested in innovative solutions for your integrated sensor technology?
Contact Dennis Kowalke by e-mail at kowalke@ifw.uni.hannover.de or by telephone on +49 511 762 5506.